Looking at a finished envelope, you may not realize all of the technology, testing, and innovation involved in creating it. There is much more than meets the eye – sizes, seams, flaps, closures. Envelopes can be one of the most critical marketing tools for your product. They may be the first impression of your brand.
Envelopes are classified based on how they open – open end or open side. Open end envelopes are characterized by the placement of the seal flap on the short end of the envelope. Here are some things you maybe didn’t know about what goes into open end envelopes.
The anatomy of an open end envelope.
Who knew there was so much that went into an envelope? The open end envelope construction is made up of several components.
- Face or Front Panel – the front of the envelope without seams. The face is the first impression most users have of the envelope.
- Back Panel – formed when the side flaps and bottom flap are folded into the envelope’s final shape. Contents are typically inserted from the back of the envelope.
- Side Flaps – fold in on their side seam to permanently secure the envelope’s ‘body.’ Inside side seams fold under the bottom flap. Outside side seams fold over the bottom flap.
- Bottom Flap – folds up from the bottom seam to permanently seal the bottom part of the envelope.
- Score – the fold line near the bottom of the seal flap. This score allows the flap to be easily folded and sealed to the envelope. Side and bottom seams are scored during the manufacturing process to ensure folding precision.
- Throat – the opening at the top of the envelope. The size of the throat is measured from the center of the score line to the top of the folded bottom flap.
- Shoulders – the two far edges of the throat where the side flaps crease with the top flap. Shoulder design determines how much the envelope can open at the throat and affects the ease of inserting contents. Angled shoulders create a scooped throat, which makes for ideal machine insertion.
- Seal Flap – the top flap that folds to close the envelope. Seal flap designs can vary based on application and filling process.
- Seal Gum – the adhesive applied to the seal flap to secure the closure once the contents are placed inside
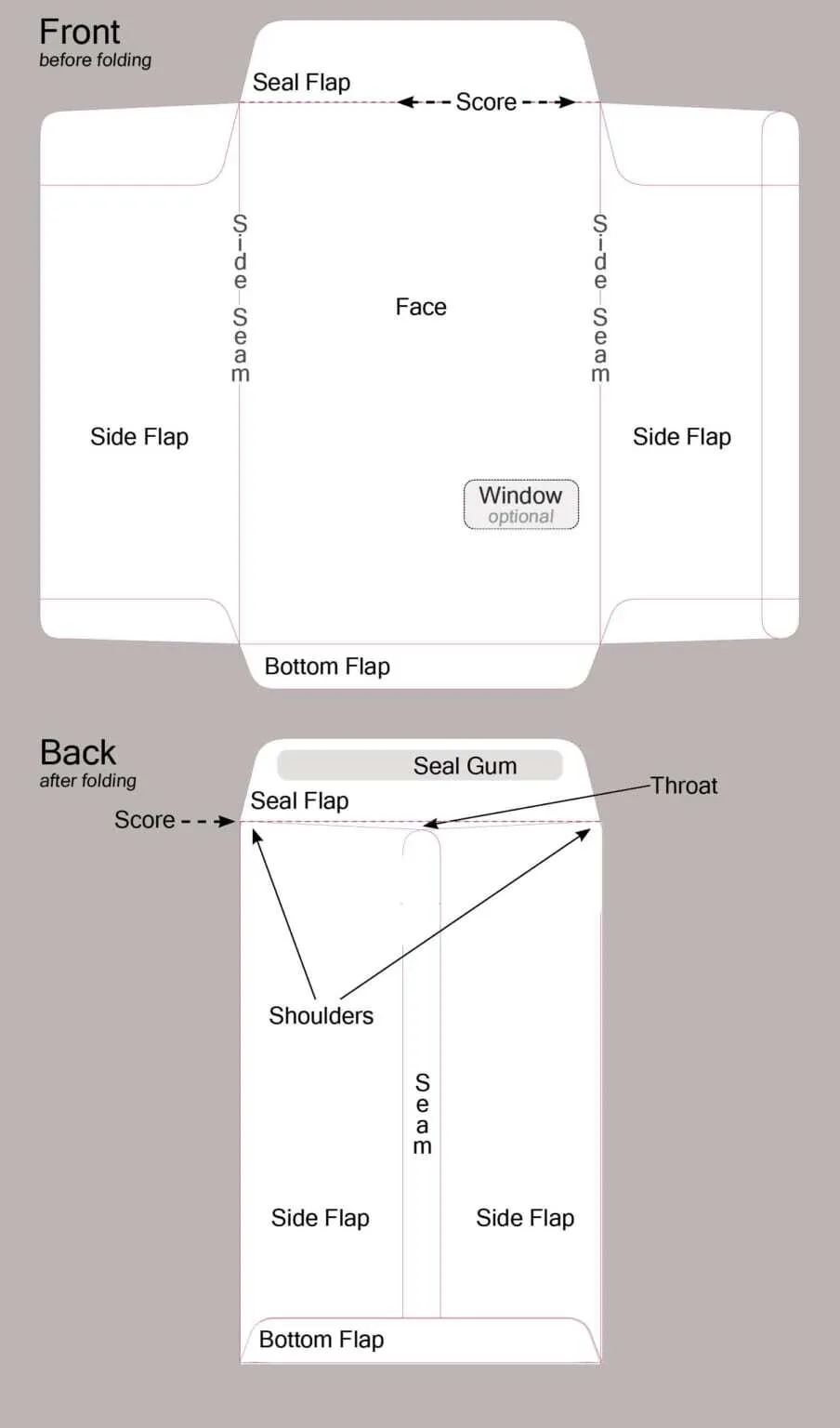
Seam styles can vary depending on envelope use needs.
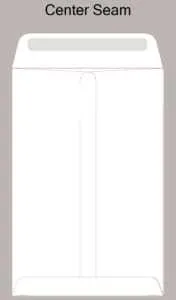
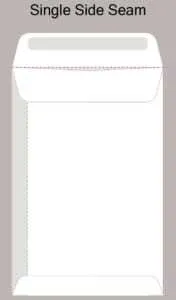
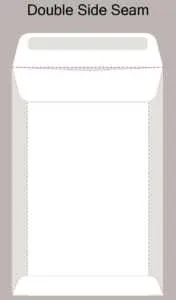
Each type of seam provides different benefits based upon the end use. The two seam styles used most often in the construction of open end envelopes are side and center seams.
Center Seams join the two side flaps together at the center of the envelope. The seam line is slightly off center to allow the adhesive to join the seams. Center seams are ideal for automated inserting equipment because their location down the center provides for maximum opening of the throat at both shoulders plus excellent strength at the side seams.
The added strength of center seams aids in the durability of storing or mailing thicker or heavier inserts such as booklets, brochures, insurance policies, and financial statements.
Side Seams seal the back of the envelope when folded. They can be oriented on the left or right side of the back panel. Double Side Seams tuck underneath the back panel. Side seams are best when printing on the outer envelope to offer additional continuous ‘real estate’ for marketing. This seam style ensures the printing aligns perfectly.
Side seam constructions are not recommended for all automated filling equipment. The shoulder on the seam side of the envelope may not open the throat of the envelope enough for the automated insertion process to run smoothly.
How closures keep contents secure.
The seals hold the envelope components together and ultimately close the flap. The adhesive (also known as gum) used for the envelope closure is available in varying bond strengths to meet specific end use applications. Because the flap is open and exposed until filling, storage considerations are important. Adhesive shelf life is affected by the temperature and humidity where the envelopes are stored.
- Back Gums are the permanent adhesives used on the bottom and side flaps to form the envelope’s ‘body’ during the manufacturing process. They are designed to hold the flaps together for the life of the envelope.
- Remoistenable Gums are a common envelope sealing method. The adhesive activates when the water-soluble gum is moistened. Gummed envelopes are suitable for automatic inserting and sealing equipment. This gum can be applied to the flap in either full or split gum. In split gumming, the gum pattern is interrupted and helps prevent the flap from sticking to the back panel during storage. Remoistenable gums may have issues with losing their bond under prolonged heat conditions; but stored correctly, these gums can last for several years. Gums are typically made from a blend of synthetic resin and dextrin, which makes them biodegradable.
- Latex Gums are self-sealing adhesives applied to the flap and the back of the envelope. Made from natural or synthetic elastomers, latex does not require moisture to activate the adhesive. The self-sealing glue adheres to itself – when pressed together, the glue on the flap sticks to the glue on the back of the envelope to form the seal. Different additives and resins provide various degrees of adhesion. Self-Adhesive Latex is a permanent single-use gum. The gum line typically covers the majority of the flap and the sealant only works once. When pressure is applied upon closing, the gums adhere to one another, and the envelope is torn when peeled open. Resealable Latex forms a lighter bond, which allows for sealing and resealing. The gum line is usually smaller to enable easier opening. Storage considerations are especially important for this adhesive’s limited shelf life.
- Peel-&-Seal envelope closures combine a self-adhesive gum covered with a protective release liner. The liner strip is removed to reveal the adhesive. The pressure-sensitive seal offers a quick, easy, and clean closure, without moistening. The closures are permanent and offer tamper-evident benefits. JBM Packaging’s trademarked Pull ‘N Stick® acts as a security seal – it’s nearly impossible to open the envelope without tearing the flap.
Many different sizes.
Open end envelopes of almost any size can be manufactured. But some sizes are more common. The envelope is measured with the shorter dimension noted first. From small coin envelopes to large catalog envelopes. Standard coin envelopes are named in industry terms with numbers – from #00 to #7. Uses range from storing coins and cash to collecting seeds and receipts. Larger open end envelopes, such as catalog and policy envelopes, are typically manufactured in sizes up to 10” x 13”. These envelopes are perfectly sized mailers for larger items such as financial and insurance documents, catalogs, and brochures. The center seam on the back of the envelope makes it more durable for holding and mailing thick or heavyweight materials.
Reimagine what small open end envelopes can do.
That’s what we do at JBM Packaging. We believe the envelope should get just as much attention as what goes inside of it. From catalog and coin envelopes, to card sleeves and collection envelopes, we offer stock and custom printed open end designs. We began as an envelope company 35 years ago. It’s where we got our start. As the largest manufacturer of small open end envelopes, we print and manufacture envelopes for financial services, medical, hospitality, retail, food, and agriculture applications around the world.
But beyond coin envelopes and drive-up bank envelopes. We see open end envelopes as two-dimensional packaging solutions for new applications in numerous markets. Small envelopes. Infinite possibilities.